Is your vehicle struggling to start, stalling unexpectedly, or showing warning lights on the dashboard? These frustrating issues might point to a failing crankshaft position sensor—a small but crucial component that monitors your engine’s rotational speed and position. When this sensor malfunctions, it can wreak havoc on your car’s performance and leave you stranded at the worst possible moments.
We’ve helped countless drivers identify and address crankshaft position sensor problems before they escalate into costly repairs. In this guide, we’ll walk you through the seven telltale symptoms that indicate your crankshaft position sensor is on its last legs. Understanding these warning signs can save you time, money, and the headache of unexpected breakdowns.
Understanding the Role of a Crankshaft Position Sensor
The crankshaft position sensor serves as a critical component in modern vehicle engines, monitoring the position and rotational speed of the crankshaft. Located near the main pulley or flywheel, this electronic device generates signals that the engine control unit (ECU) uses to determine ignition timing and fuel injection sequences. These precise measurements ensure your engine fires at exactly the right moment for optimal performance.
Your vehicle’s ECU relies on this sensor’s data to make split-second adjustments to engine timing. Without accurate information from the crankshaft position sensor, the ECU can’t properly synchronize fuel injection and spark plug firing—leading to many drivability issues. The sensor typically consists of a magnetic pickup or Hall effect sensor that creates electrical pulses as the crankshaft rotates.
Most modern vehicles employ this sensor as part of a sophisticated engine management system. As the toothed wheel on the crankshaft rotates past the sensor, it creates a changing magnetic field that generates voltage signals. These signals create a exact pattern the ECU interprets to determine the exact position of the pistons and crankshaft rotation speed.
Engine performance depends heavily on the precise timing this sensor provides. Proper air-fuel mixture delivery and spark timing rely on accurate crankshaft position data. When functioning correctly, the sensor helps maintain smooth idling, consistent acceleration, and optimal fuel efficiency while reducing harmful emissions.
Engine Starting Problems: The First Warning Sign
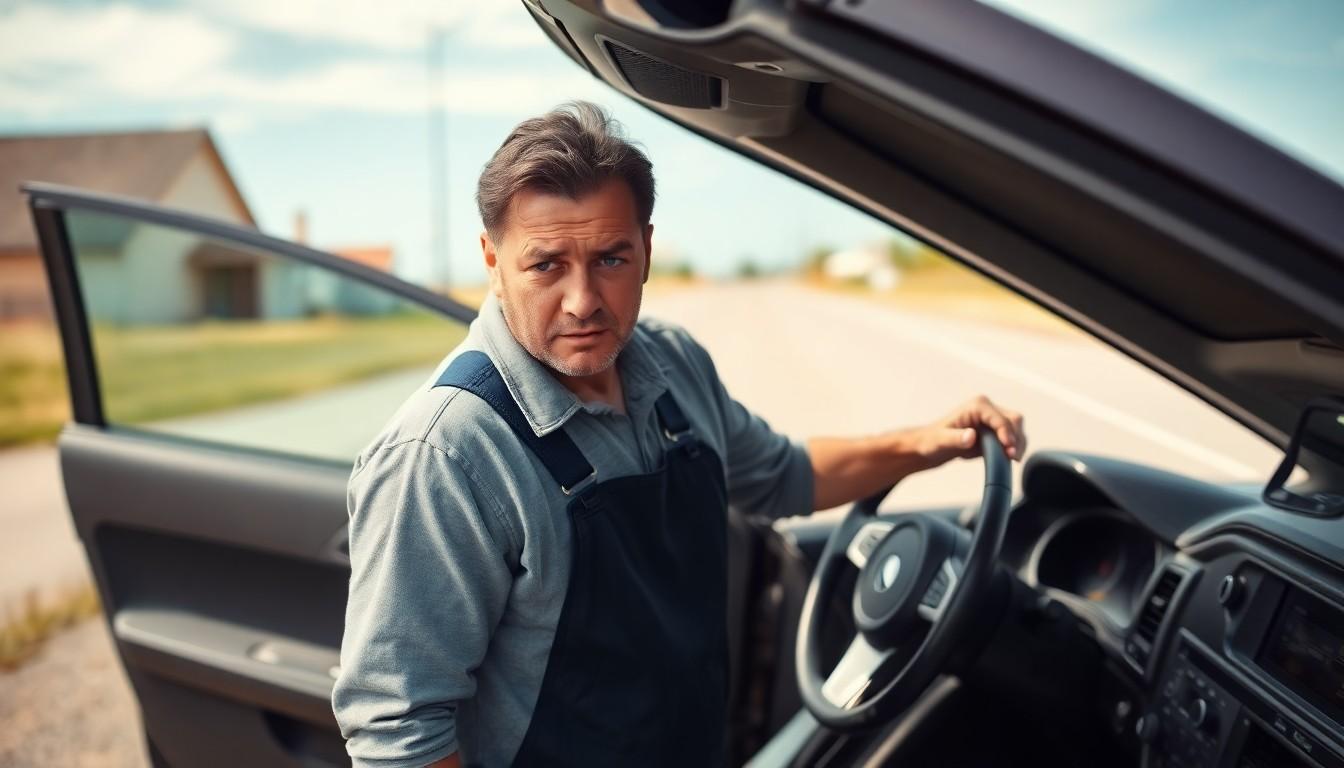
Prolonged cranking or complete failure to start represents the most common symptom of a faulty crankshaft position sensor. Engines typically require extra time to turn over when this sensor malfunctions, as the powertrain control module (PCM) struggles to receive accurate positional data. Many drivers notice this problem manifests as turning the key and hearing the engine crank repeatedly without starting.
Kickbacks or backfiring often accompany starting issues, particularly during initial startup attempts. These alarming sounds occur because the sensor isn’t properly synchronizing the ignition timing with the crankshaft’s position. Your vehicle might produce distinctive popping and banging noises during attempted starts—clear indicators of crankshaft position sensor failure.
The starting problem typically progresses from intermittent to consistent over time. Initially, you’ll experience occasional difficult starts that become more frequent as the sensor deteriorates further. Cold mornings often exacerbate these symptoms, making the problem more noticeable when temperatures drop. Engine starting issues serve as an early warning sign that shouldn’t be ignored, as they frequently precede complete system failure.
Check Engine Light Illumination
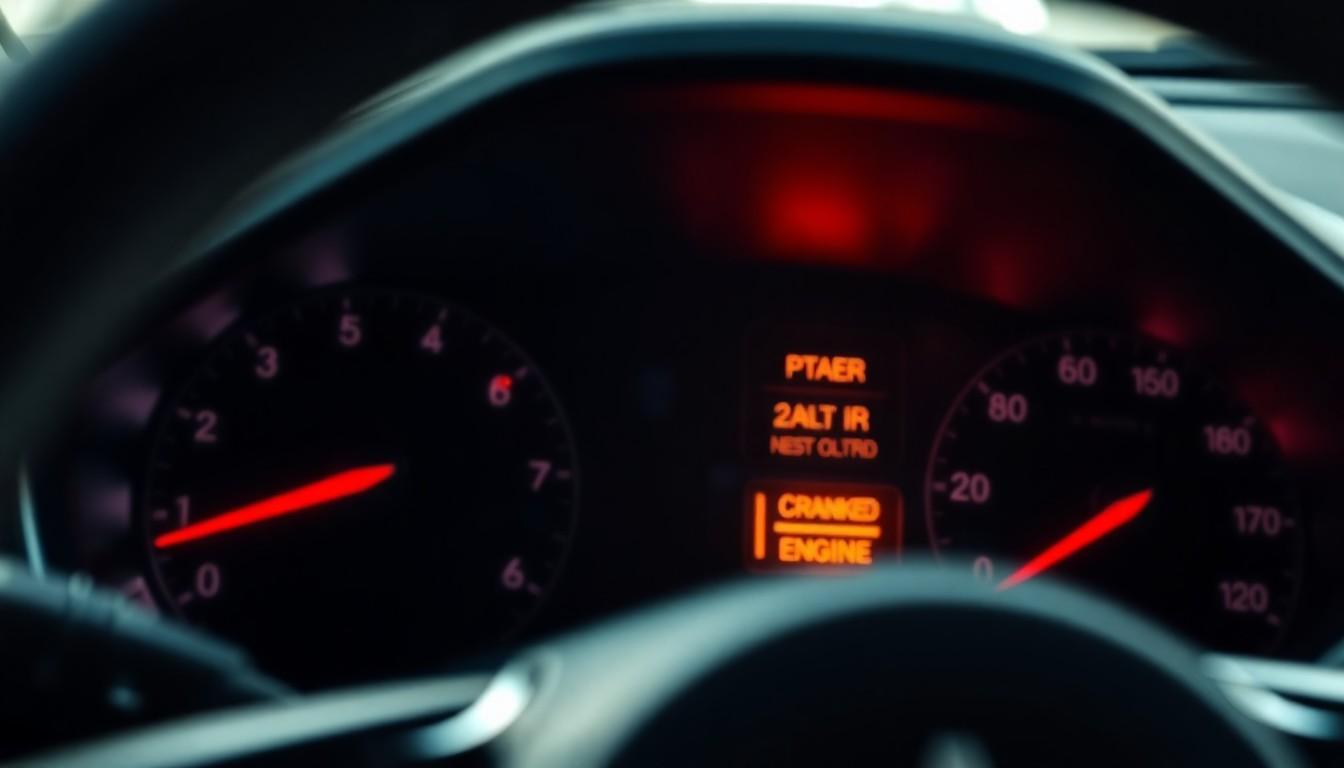
The Check Engine Light serves as your vehicle’s primary warning system when the crankshaft position sensor begins to fail. This dashboard indicator illuminates when the sensor transmits incorrect signals or no signals at all to your vehicle’s computer system. Many drivers notice this warning light as the first indication of a potential crankshaft position sensor issue. The engine control module constantly monitors sensor performance and triggers this warning light when it detects inconsistencies in the data stream.
Modern vehicles rely on precise timing information from the crankshaft position sensor to maintain optimal engine operation. When this communication breaks down, your car’s onboard diagnostics system immediately flags the problem. Diagnostic trouble codes related to crankshaft sensor failures often include P0335 (Crankshaft Position Sensor Circuit Malfunction) and P0336 (Crankshaft Position Sensor Range/Performance). These exact codes help technicians pinpoint the exact nature of the sensor malfunction.
It’s important to note that while a glowing Check Engine Light doesn’t necessarily mean your crankshaft position sensor has failed, it definitely warrants prompt investigation. The warning light might appear intermittently at first before becoming a permanent fixture on your dashboard as the sensor deteriorates further. Professional diagnostic equipment can quickly determine if the crankshaft position sensor is indeed the culprit behind the illuminated warning light.
Unexpected Engine Stalling
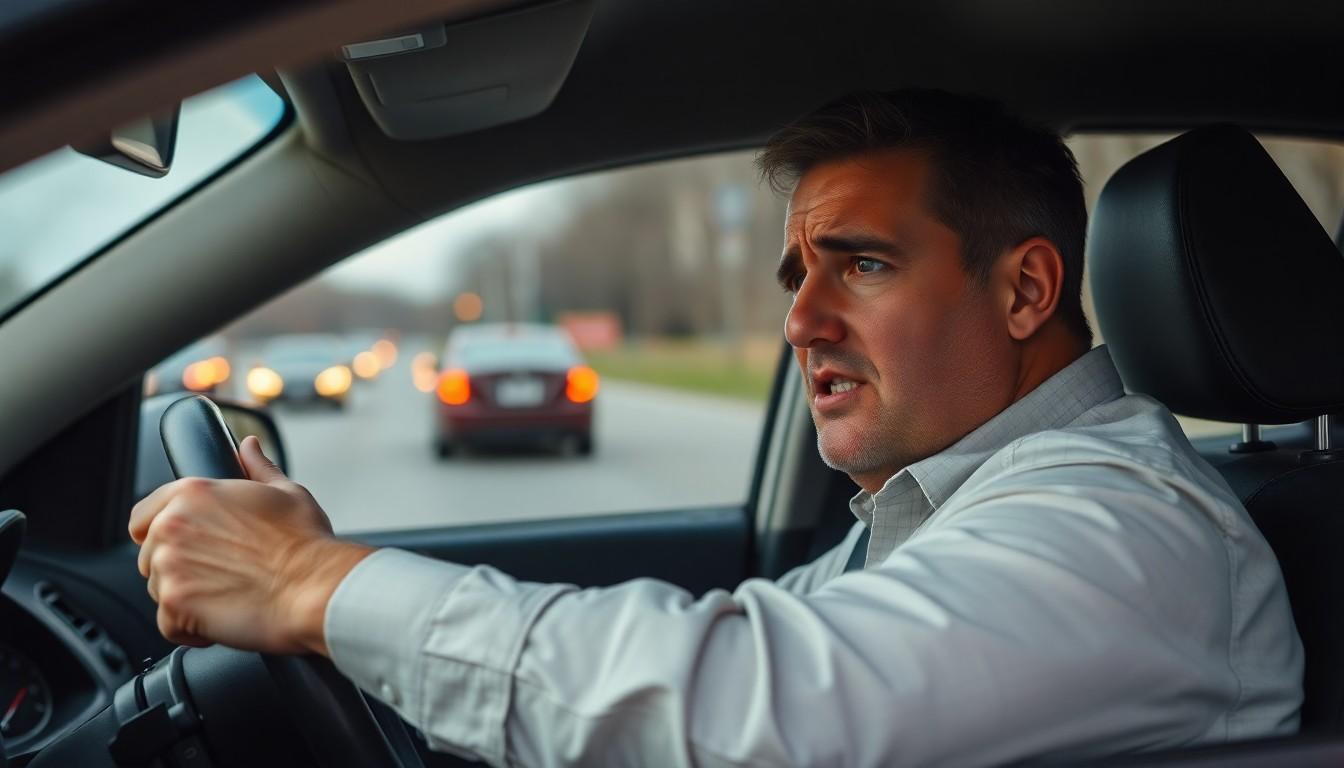
Intermittent stalling represents one of the most common and dangerous symptoms of a failing crankshaft position sensor. Your vehicle might shut off completely without warning while you’re driving, creating potentially hazardous situations on busy roads or highways. This sudden stalling occurs because the erratic signals from a malfunctioning sensor confuse the engine control unit, disrupting the precise timing needed for combustion.
Many drivers report their vehicles stalling at low speeds initially, such as when approaching a stop sign or idling at a traffic light. The engine’s computer relies on accurate crankshaft position data to maintain proper fuel injection and spark timing sequences. When this data becomes inconsistent or disappears entirely, the engine can’t maintain operation and simply shuts down.
The unpredictable nature of this symptom makes it particularly troublesome. Your vehicle might run perfectly fine for days, then suddenly stall multiple times in a single trip. Temperature changes often exacerbate the problem, with many sensors showing increased failure rates during extreme hot or cold conditions.
Restarting after an unexpected stall typically gets progressively more difficult as the sensor deteriorates further. You’ll notice this pattern evolving—what begins as occasional stalling eventually becomes more frequent until the vehicle becomes completely unreliable. This escalating pattern serves as a critical warning sign that shouldn’t be ignored.
Safety concerns amplify the importance of addressing this symptom quickly. Losing power steering and brake assist during unexpected stalling creates dangerous driving conditions, especially at higher speeds or in heavy traffic. Diagnostic testing can confirm if the crankshaft position sensor is indeed the culprit behind these intermittent stalling episodes.
Poor Acceleration and Performance Issues
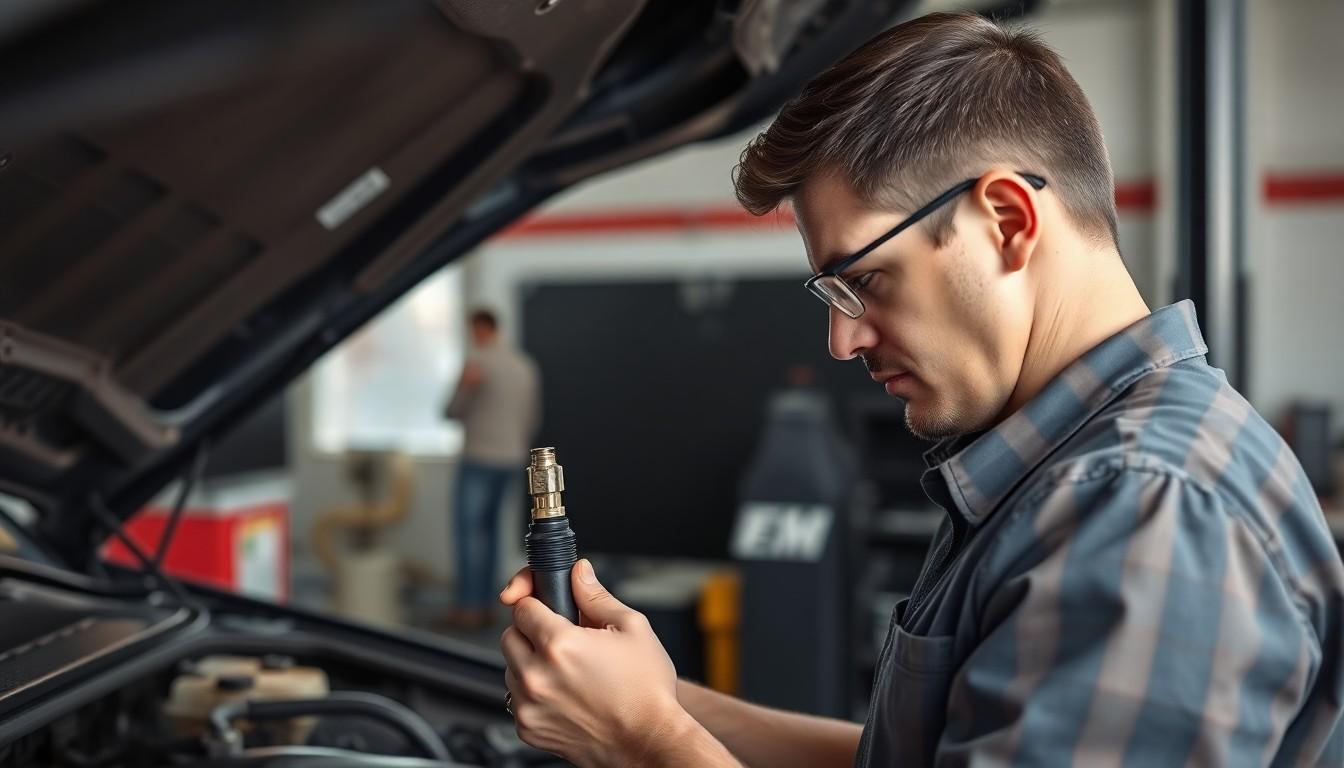
A failing crankshaft position sensor often manifests as noticeable power loss during acceleration. When this sensor malfunctions, the engine computer receives inaccurate timing signals for fuel injection and spark timing, resulting in sluggish throttle response and reduced engine performance. Cars with this issue struggle to maintain consistent power output, particularly when attempting to accelerate from a stop or while overtaking on highways.
Engine misfires frequently accompany poor acceleration, creating a jerky driving experience that’s impossible to ignore. These misfires occur because the erratic signals from a defective crankshaft position sensor lead to miscalculated fuel injector pulse and spark timing. Drivers typically notice hesitation when pressing the gas pedal, followed by a sudden surge of power as the engine computer attempts to compensate for the incorrect timing data.
Fuel economy suffers significantly with a bad crankshaft position sensor. The engine’s decreased efficiency from constant misfires and rough running conditions leads to increased fuel consumption. Also, advanced fuel-saving technologies like variable valve timing and cylinder deactivation may fail to function properly without accurate crankshaft position data, further reducing your vehicle’s gas mileage.
Intermittent performance problems create frustrating driving experiences when dealing with a failing sensor. The engine might stumble or shake unexpectedly, especially under load conditions such as climbing hills or accelerating with passengers. These performance inconsistencies stem directly from the sensor’s inability to provide reliable data to the engine control module, causing the computer to make inappropriate adjustments to critical engine parameters.
Engine roughness at idle represents another telltale sign of crankshaft position sensor failure. Your vehicle might vibrate excessively or run unevenly when stopped at traffic lights or in park. The rough idle occurs because the engine computer can’t properly synchronize fuel delivery and spark timing without accurate crankshaft position information, leading to combustion inefficiencies even at low RPMs.
Erratic Idling Behavior
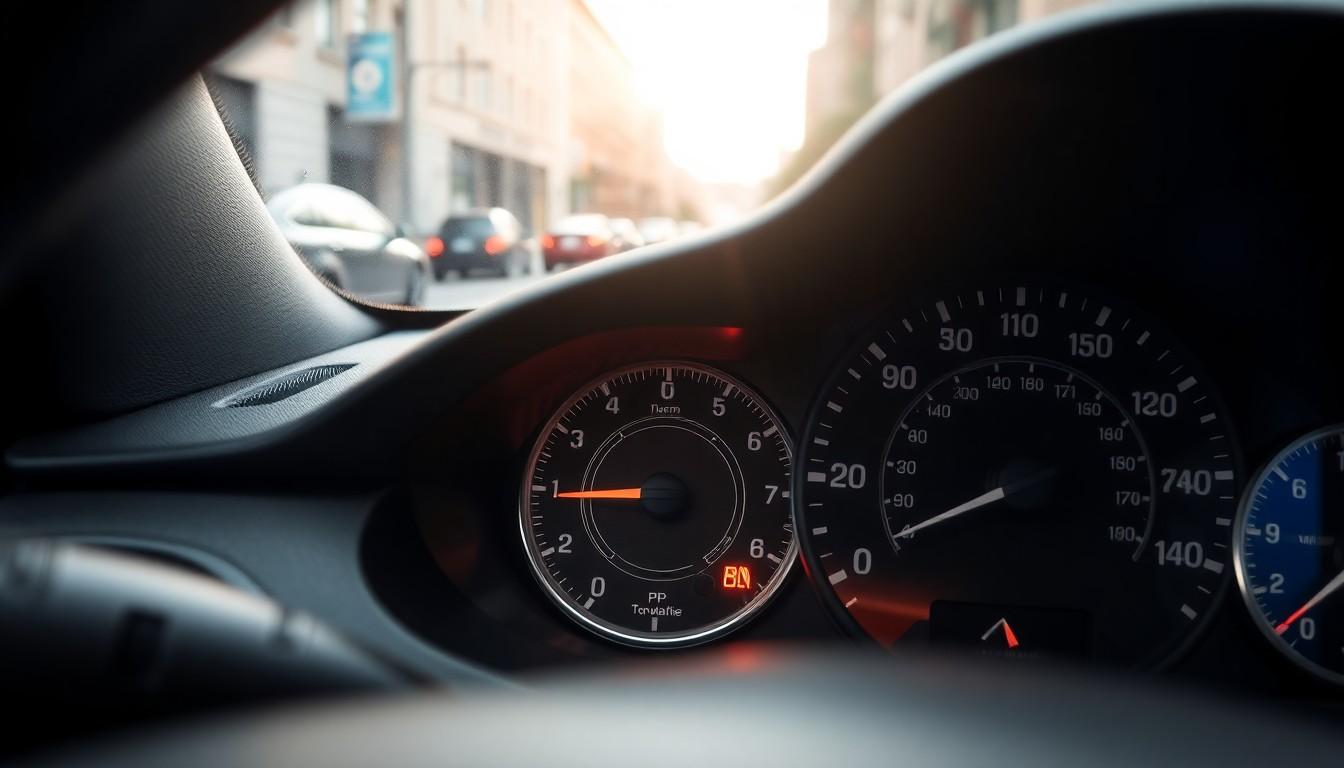
Erratic idling behavior manifests when your engine runs at inconsistent speeds while the vehicle is stationary. Irregular RPM fluctuations during idle often indicate a failing crankshaft position sensor sending incorrect data to the engine control unit. The engine computer struggles to maintain proper timing for fuel injection and ignition when receiving faulty crankshaft position information. Many drivers notice their tachometer needle bouncing unpredictably between different RPM readings while idling at stoplights.
Unstable idling typically occurs because the sensor can’t accurately track the crankshaft’s position and rotational speed. Your engine might suddenly dip below normal idle speed or unexpectedly surge higher without any throttle input. These idle fluctuations frequently accompany other drivability issues like hesitation, stalling, or rough running conditions. Cold mornings or hot weather conditions tend to exacerbate these erratic idle symptoms when the sensor is deteriorating.
The connection between crankshaft sensor failure and idle problems stems from the engine’s timing requirements. Without precise crankshaft position data, the ECU cannot synchronize fuel delivery and spark timing effectively during low-speed operation. Diagnostic scans often reveal intermittent signal errors or voltage fluctuations from the crankshaft sensor circuit during problematic idle periods. Some vehicles display more subtle symptoms like slight vibrations or minor RPM variations that gradually worsen as the sensor continues to degrade.
Increased Fuel Consumption
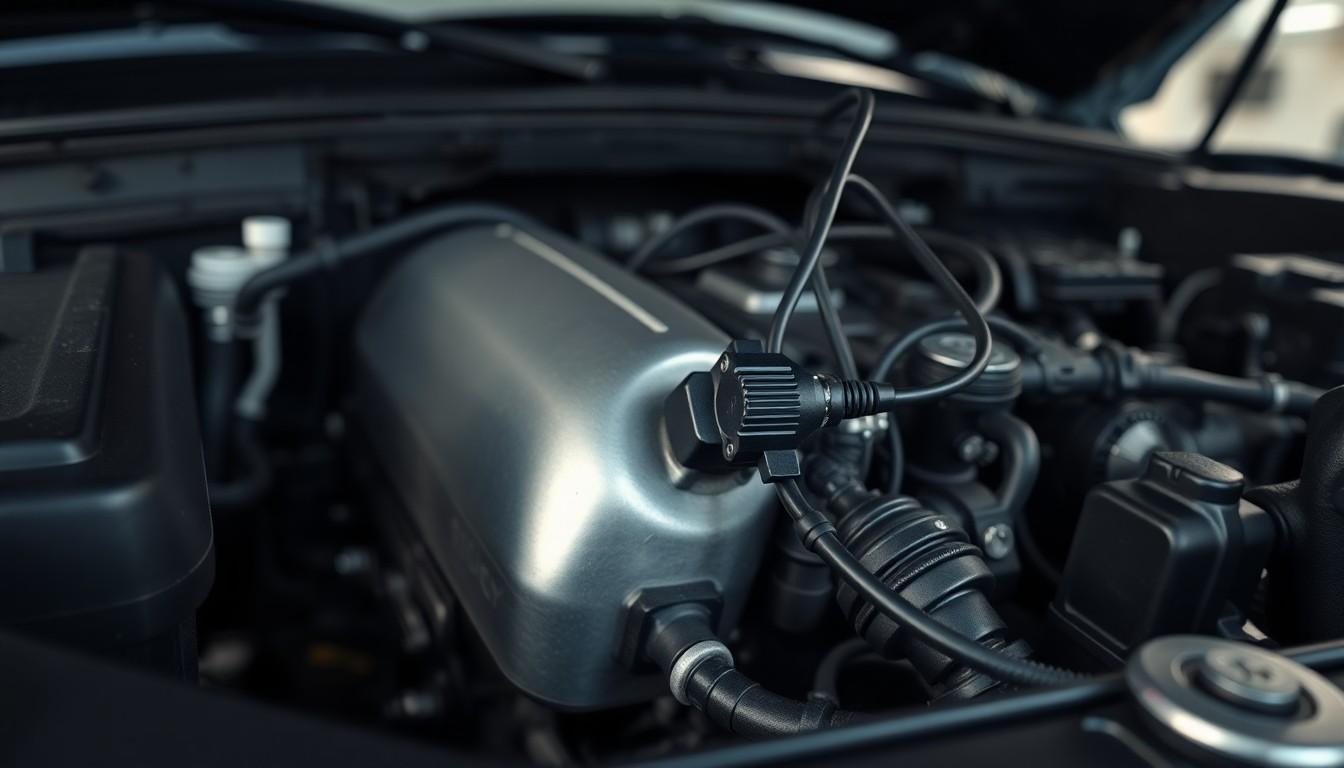
A faulty crankshaft position sensor directly impacts your vehicle’s fuel efficiency, creating a noticeable decrease in miles per gallon. This critical component helps the Engine Control Unit (ECU) optimize the timing of fuel injection and spark ignition for maximum efficiency. When the sensor malfunctions, the ECU lacks accurate data about crankshaft position and rotation speed, leading to suboptimal combustion timing.
Fuel economy typically drops by 3-4 MPG when driving with a bad crankshaft position sensor, as confirmed by diagnostic testing. The ECU compensates for missing or inaccurate timing signals by defaulting to a “safe mode” where it doses excess fuel to prevent engine damage. This conservative fuel management strategy prioritizes keeping the engine running over maintaining efficiency.
Many drivers notice they’re filling up their tanks more frequently before identifying the underlying sensor issue. The problem often becomes apparent during highway driving when fuel consumption should be at its most efficient. Instead, the engine runs rich continuously, wasting fuel and creating additional strain on engine components.
Tracking your vehicle’s fuel consumption provides an early indicator of potential crankshaft position sensor failure. The decline in efficiency happens gradually in most cases, making it easy to miss until the problem becomes severe. Regular monitoring of your vehicle’s MPG helps identify this symptom before more serious drivability issues develop.
Engine Misfires and Rough Running
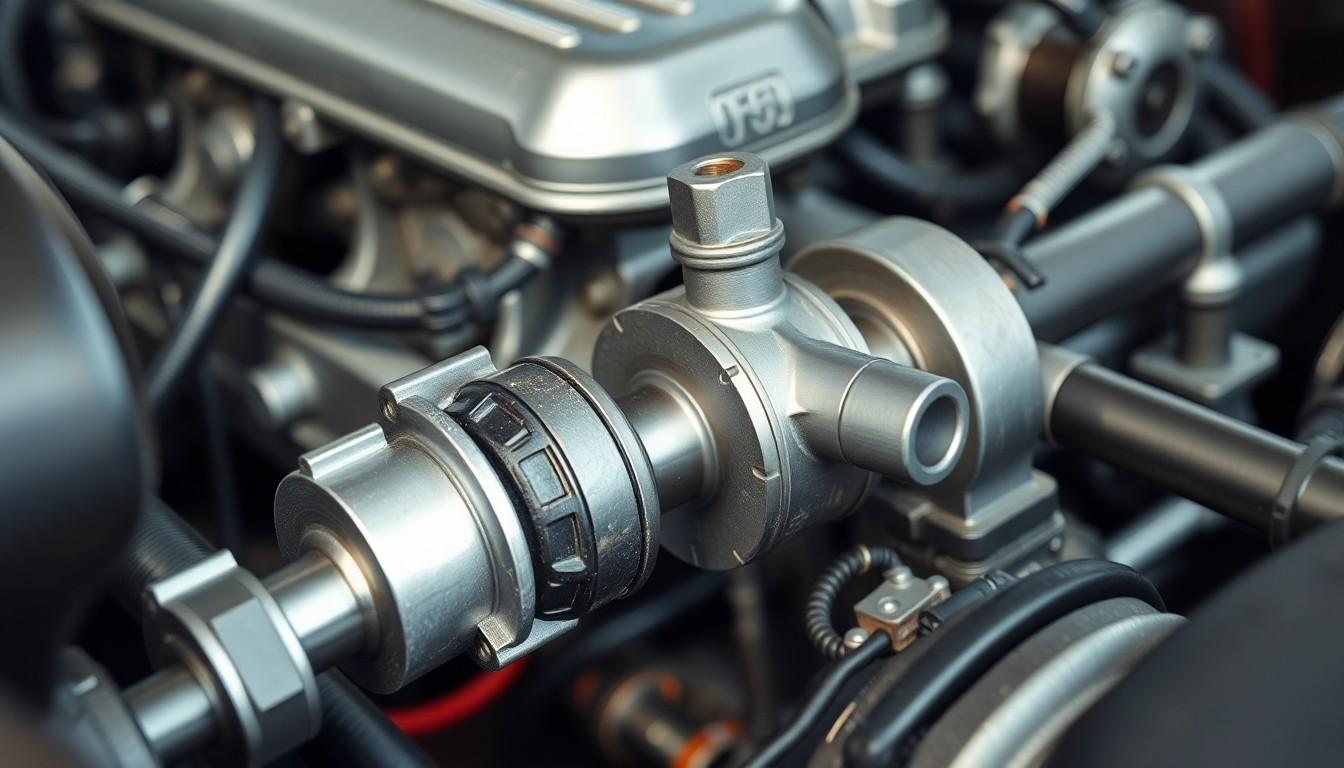
Engine misfires and rough running are telltale indicators of a failing crankshaft position sensor (CKP). When this sensor transmits erratic signals to the Powertrain Control Module (PCM), the computer miscalculates critical timing for fuel injection and spark delivery. The inconsistent signals cause the engine to misfire, creating a noticeable shaking or stumbling sensation, particularly when the vehicle is under load.
Drivers experience these symptoms as:
- Subtle vibrations through the steering wheel or seat during acceleration
- Stumbling or hesitation when pressing the gas pedal
- Jerky performance especially when climbing hills or overtaking
- Reduced power during normal driving conditions
The rough running occurs because the PCM relies on precise crankshaft position data to synchronize the ignition and fuel systems. Without accurate timing information, the engine’s cylinders fire at incorrect intervals, disrupting the combustion sequence. This desynchronization not only affects performance but also contributes to increased emissions and potential damage to catalytic converters.
Fuel and spark delivery problems resulting from a bad CKP sensor often worsen progressively. Initially, drivers might notice occasional hiccups or brief power losses, but as the sensor deteriorates further, the misfires become more frequent and severe. Engine roughness typically intensifies during exact operating conditions such as cold starts or when the engine reaches normal operating temperature.
Many vehicles with faulty crankshaft position sensors display inconsistent symptoms—running smoothly one moment, then suddenly misfiring the next. This unpredictability stems from the sensor’s intermittent failure patterns, making diagnosis challenging without proper testing equipment.
How to Diagnose a Faulty Crankshaft Position Sensor
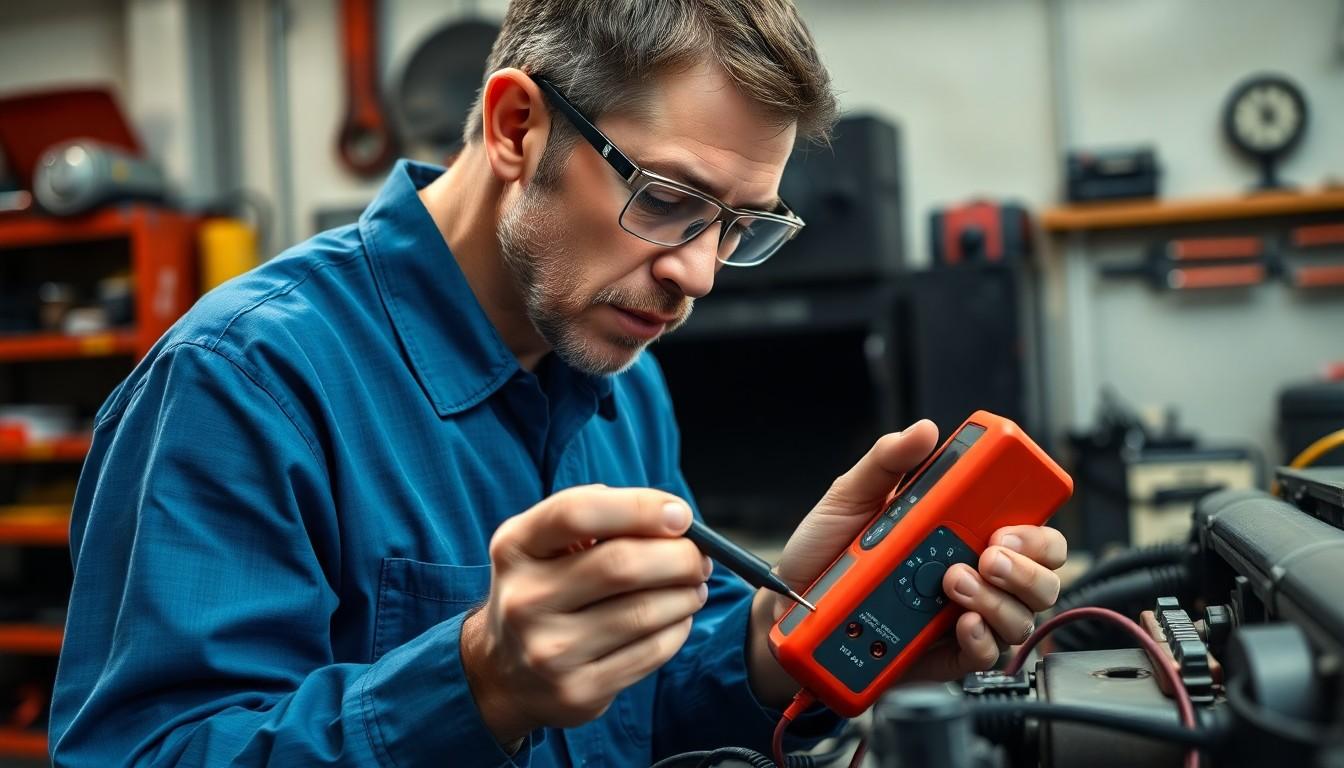
Diagnosing a crankshaft position sensor problem requires a systematic approach to identify the root cause. Our diagnosis process begins with a visual inspection of the sensor and its wiring for visible damage or corrosion. Next, specialized diagnostic equipment like an OBD2 scanner helps retrieve any trouble codes stored in the vehicle’s computer, while more advanced tools can test the sensor’s output signal against manufacturer specifications.
DIY Testing Methods
DIY crankshaft position sensor testing starts with locating the sensor near the crankshaft—typically found at the front of the engine by the crankshaft pulley, on the engine block, or near the transmission bell housing. After disconnecting the electrical connector, use a multimeter set to the resistance setting to test the sensor terminals. Normal resistance readings generally fall between 200 to 1,200 ohms, but always compare your results with specifications in your vehicle’s service manual. Carefully inspect all wiring connected to the sensor for signs of fraying, melting, or corrosion that could interrupt the signal. Testing the sensor with an oscilloscope provides more detailed analysis of the sensor’s performance during engine operation, allowing you to visualize the actual signal patterns being produced.
When to Seek Professional Help
Professional assistance becomes necessary when dealing with intermittent sensor symptoms that are difficult to reproduce during home testing. Technicians possess specialized diagnostic equipment that can monitor sensor performance under various operating conditions. Complex sensor installation procedures on certain vehicle models may require professional expertise, especially when the sensor location is difficult to access or requires special tools. Mechanics can also perform comprehensive testing to ensure the problem isn’t caused by related components like the wiring harness or engine control module. If your initial diagnosis attempts reveal inconsistent results or if replacing the sensor doesn’t resolve the issue, professional diagnostic services can save time and prevent unnecessary parts replacement.
Replacement Costs and Considerations
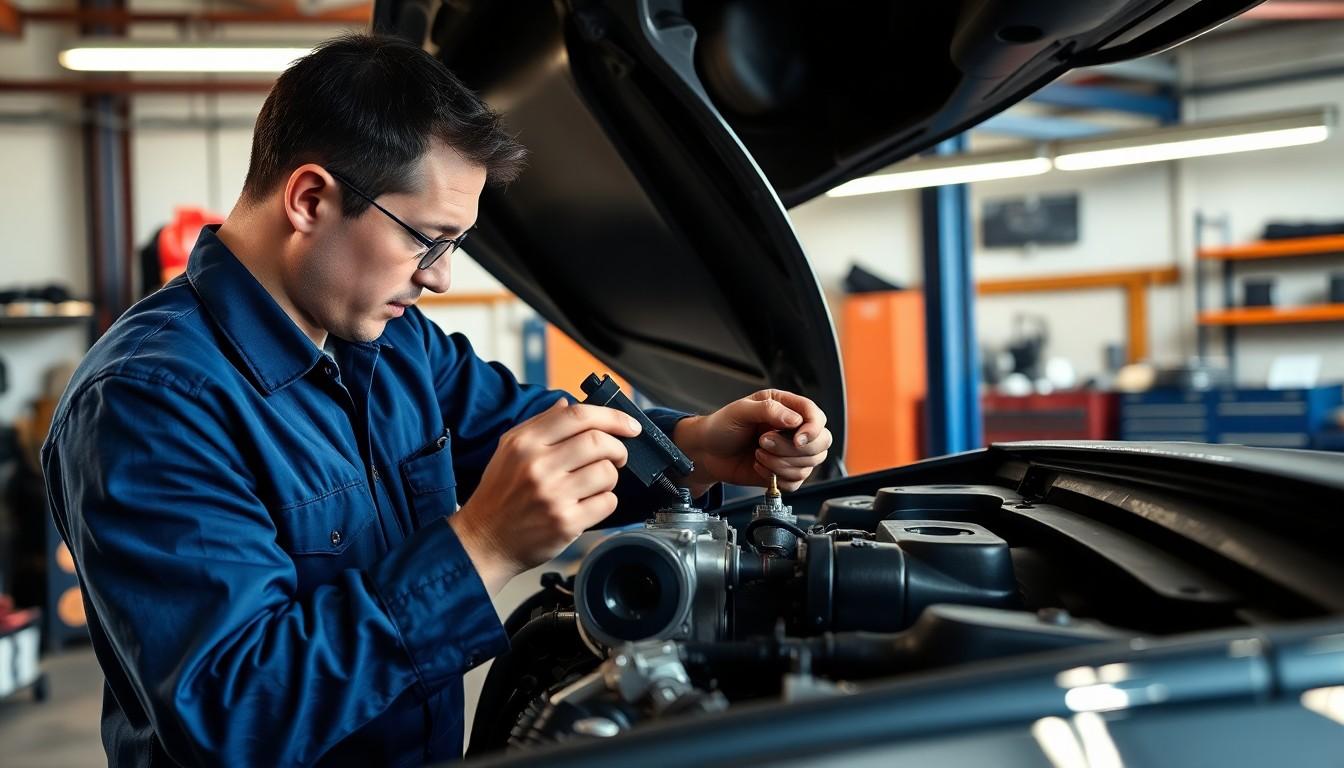
Replacing a crankshaft position sensor involves both parts and labor costs that vary depending on your vehicle’s make and model. The sensor itself typically costs between $40 and $150, with higher-end or luxury vehicles commanding premium prices for OEM parts. Labor charges can range significantly from $100 to $700, reflecting the accessibility of the sensor’s location and the complexity of the replacement procedure.
Most vehicle owners can expect to pay a total of $100 to $400 for a complete crankshaft position sensor replacement. Luxury vehicles and complex engine designs often push this cost higher, potentially reaching $700 or more for the entire service. BMW models, for example, generally fall in the $200 to $400 range, while Hyundai and Kia vehicles typically cost between $100 and $300 for the same repair.
Several factors influence the final cost of your crankshaft position sensor replacement:
- Vehicle Accessibility: Sensors that are difficult to reach require more labor time
- Dealer vs. Independent Shop: Dealerships typically charge more than independent mechanics
- OEM vs. Aftermarket Parts: Original equipment manufacturer sensors cost more but may provide better reliability
- Geographic Location: Labor rates vary significantly based on your region
- Vehicle Make and Model: European luxury vehicles generally incur higher replacement costs than domestic or Asian models
DIY replacement can save substantial labor costs for those with mechanical experience. The procedure requires basic tools and mechanical knowledge, with the most challenging aspect often being accessing the sensor’s location. Many crankshaft position sensors are situated near the engine’s flywheel or behind the crankshaft pulley, making replacement more complicated in some vehicles than others.
Conclusion
Recognizing the seven symptoms of a failing crankshaft position sensor is crucial for maintaining your vehicle’s performance and safety. By staying alert to warning signs like starting difficulties check engine lights unexpected stalling poor acceleration erratic idling increased fuel consumption and engine misfires you’ll be better equipped to address issues before they escalate.
Don’t ignore these symptoms as they often worsen over time leading to complete engine failure and potentially dangerous driving situations. Whether you choose DIY diagnostics or professional help prompt attention to these warning signs can save you from costly repairs and roadside emergencies.
Remember that timely replacement of a faulty sensor is significantly more affordable than repairing the extensive damage that can result from continued operation with a failing component.
Frequently Asked Questions
What is a crankshaft position sensor?
A crankshaft position sensor is an electronic device that monitors the position and rotational speed of your vehicle’s crankshaft. Located near the main pulley or flywheel, it sends crucial signals to the engine control unit (ECU) that determine ignition timing and fuel injection sequences. This component is essential for optimal engine performance, smooth idling, and fuel efficiency.
What are the main symptoms of a failing crankshaft position sensor?
The main symptoms include difficulty starting your vehicle, unexpected engine stalling, illuminated check engine light, poor acceleration and performance, erratic idling behavior, increased fuel consumption, and engine misfires or rough running. These issues typically worsen over time and may initially appear intermittently before becoming more consistent.
Why is my car having trouble starting?
Starting problems are a primary warning sign of a faulty crankshaft position sensor. When the sensor fails, your engine may experience prolonged cranking or completely fail to start because the powertrain control module isn’t receiving accurate positional data. You might also notice kickbacks or backfiring during startup attempts, with problems often worsening in cold temperatures.
Can a bad crankshaft sensor cause stalling?
Yes, a failing crankshaft position sensor can cause unexpected engine stalling while driving, which is particularly dangerous at high speeds. This happens because erratic signals disrupt the timing needed for combustion, leading to complete engine shutdown. Stalling typically becomes more frequent over time and restarting after a stall becomes increasingly difficult.
Will the check engine light come on with a bad crankshaft sensor?
Yes, the check engine light typically illuminates when the crankshaft position sensor transmits incorrect or no signals to the vehicle’s computer system. Diagnostic trouble codes related to sensor failures (such as P0335 and P0336) will be stored in the system. Initially, this warning light may appear intermittently before becoming permanently lit.
How does a failing sensor affect fuel economy?
A faulty crankshaft position sensor can significantly reduce fuel efficiency, often decreasing your miles per gallon by 3-4 MPG. This happens because the ECU defaults to a “safe mode” that uses excess fuel when it doesn’t receive accurate timing data. The problem is most noticeable during highway driving, where fuel consumption should be optimal.
How much does it cost to replace a crankshaft position sensor?
Replacement costs typically range from $100-$400 total, with the sensor itself costing between $40-$150 and labor charges ranging from $100-$700 depending on accessibility. Luxury vehicles generally cost more to repair. DIY replacement can save on labor costs if you have mechanical experience, though sensor access can be challenging in some vehicles.
How is a faulty crankshaft position sensor diagnosed?
Diagnosis begins with a visual inspection of the sensor and its wiring for damage or corrosion. Mechanics will use an OBD2 scanner to retrieve trouble codes and test the sensor’s output signal against specifications. More advanced testing involves using a multimeter and oscilloscope to check resistance readings. For intermittent issues, professional diagnostic services are recommended.