Ever wondered what makes modern engines run smoother and last longer? The hydraulic roller camshaft is a remarkable component that’s revolutionized engine performance in recent decades. We’ll break down this engineering marvel and show why it matters to both casual drivers and performance enthusiasts alike.
When it comes to engine efficiency and longevity, not all camshafts are created equal. Hydraulic roller camshafts have become the gold standard in today’s automotive industry, replacing older flat-tappet designs with a system that reduces friction, extends engine life, and delivers more consistent performance. They’re a game-changer that works behind the scenes to maximize your vehicle’s potential.
Understanding Hydraulic Roller Camshafts
Hydraulic roller camshafts represent a important advancement in engine technology, combining hydraulic lifters with roller tips to optimize valve operation. These specialized components work by using oil pressure to maintain zero valve lash automatically while the roller tip follows the cam lobe profile with minimal friction. Unlike their flat-tappet predecessors, hydraulic roller cams feature a cylindrical roller follower that actually rolls against the cam lobe rather than sliding, dramatically reducing friction and wear.
The internal mechanism of a hydraulic roller lifter includes a small oil reservoir and plunger system that compensates for thermal expansion and wear. This self-adjusting capability eliminates the need for periodic valve adjustments that older mechanical systems required. Engineers design these camshafts with exact lobe profiles that determine valve lift, duration, and timing—critical factors that influence an engine’s power curve and operating characteristics.
Most modern production vehicles come equipped with hydraulic roller camshafts as standard equipment. These factory configurations typically prioritize fuel efficiency, emissions compliance, and smooth operation across a wide RPM range. Aftermarket performance versions offer more aggressive lobe profiles with increased lift and duration measurements, allowing enthusiasts to tailor their engines for exact performance goals such as improved low-end torque or high-RPM horsepower.
Installation of hydraulic roller camshafts requires special consideration for the supporting components. The setup includes roller lifters, appropriate valve springs, retainers, and often a exact timing chain set. Compatibility with the engine block is crucial, as some older blocks may need modifications or adapter kits to properly support the roller lifter setup. These technical requirements highlight why proper component matching remains essential for optimal performance and reliability.
The Evolution of Camshaft Technology
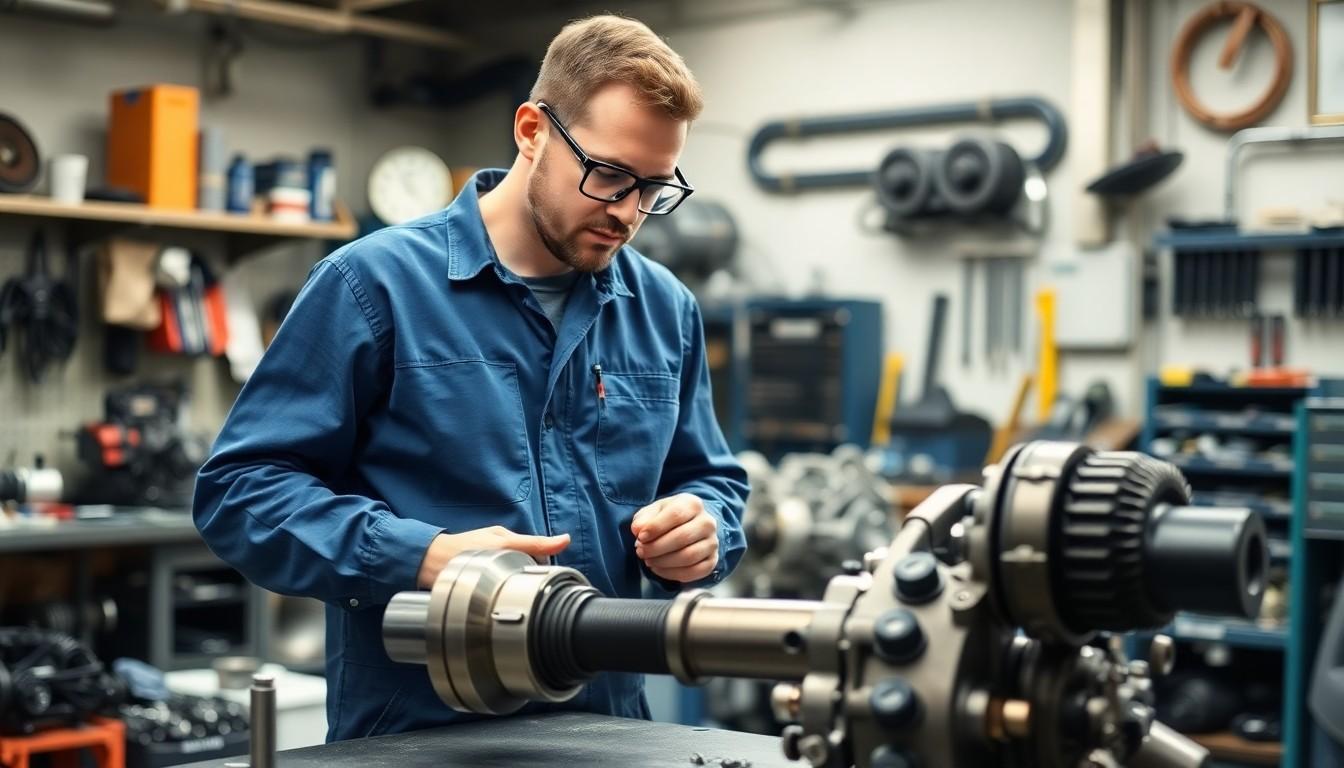
Camshaft technology has undergone important advancements over the decades, transforming how engines perform and endure. These evolutionary changes have revolutionized valve actuation systems, resulting in more efficient and reliable engines.
From Flat Tappet to Hydraulic Roller
Flat tappet camshafts represented the standard in automotive engineering for many years, utilizing simple mechanical components that wiped directly against cam lobes. These traditional designs created substantial friction between components, requiring frequent maintenance and valve train adjustments to accommodate normal wear. Engine builders faced challenges with these older systems due to their inherent limitations in high-performance applications.
Hydraulic roller camshafts emerged as the superior successor, incorporating wheel-like rollers that slide smoothly across cam lobes rather than creating the wiping action of flat tappets. This technological leap dramatically reduced internal friction while extending component life. Manufacturers began implementing these systems in production vehicles during the 1980s, and they’ve since become the industry standard for both economy and performance applications.
Benefits of Modern Design
Reduced friction stands as the primary advantage of hydraulic roller camshafts, with roller lifters decreasing resistance by 20-30% compared to flat tappet designs. This friction reduction translates directly into improved horsepower, torque, and fuel efficiency across all engine operating ranges.
Hydraulic roller systems operate with noticeably quieter performance thanks to their self-adjusting mechanisms that maintain optimal valve clearance. Engine noise decreases substantially without the metal-on-metal contact present in older designs, creating a smoother driving experience for everyday vehicles.
Maintenance requirements drop significantly with hydraulic roller camshafts since they automatically adjust for wear and thermal expansion. Owners enjoy extended service intervals without needing manual valve adjustments that were once considered routine maintenance.
Performance enthusiasts gain substantial benefits from the quicker valve motion provided by roller systems. The design allows for more aggressive cam profiles that open and close valves more efficiently, resulting in power gains throughout the RPM range. Racing engines particularly benefit from these advancements, with some applications seeing 5-10% power increases over comparable flat tappet setups.
How Hydraulic Roller Camshafts Work
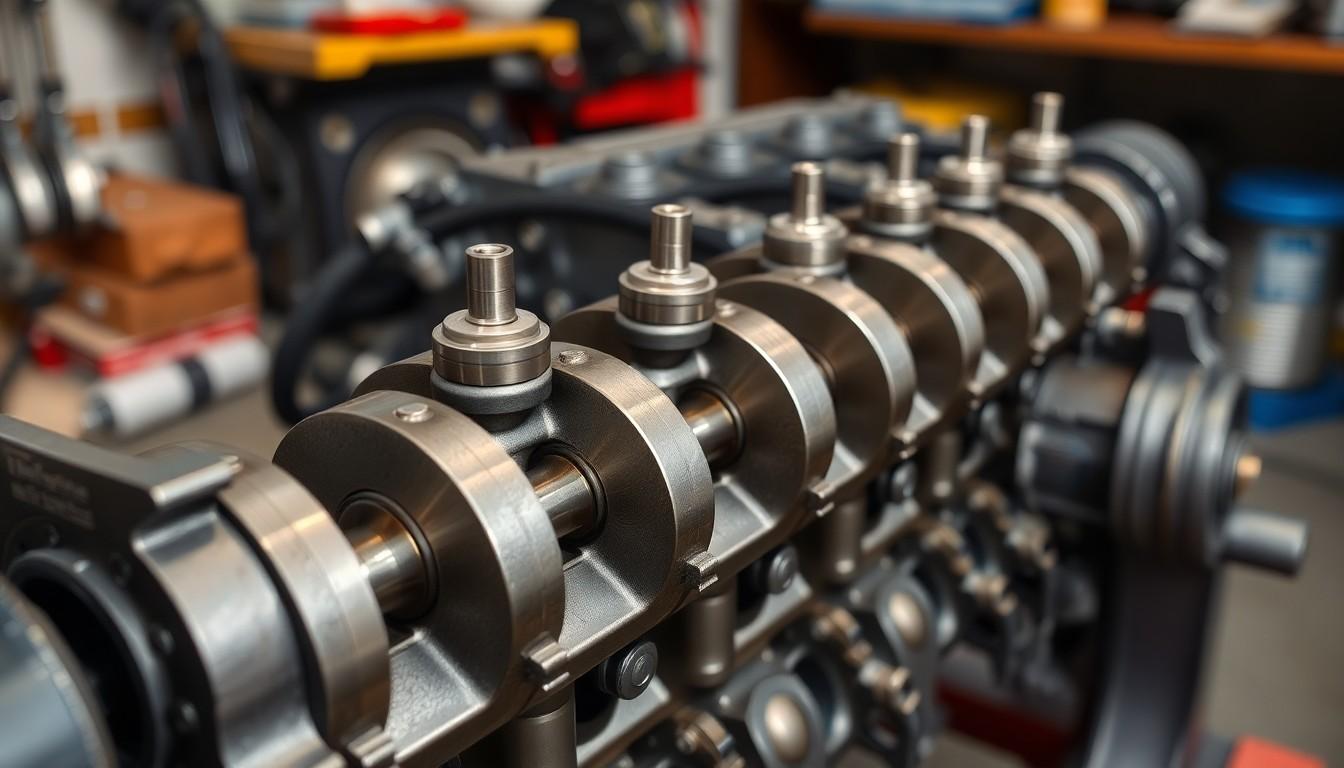
Hydraulic roller camshafts operate through a precise mechanical system that combines rotational motion with hydraulic pressure. The camshaft rotates inside the engine block, and its specifically designed lobes push against hydraulic lifters with roller tips, transferring motion through the valve train to operate the engine’s valves with exceptional precision.
The Hydraulic Lifter Mechanism
Hydraulic lifters contain an ingenious self-adjusting system that automatically maintains optimal valve clearance. Inside each lifter, a hydraulic plunger uses engine oil pressure to eliminate any lash between components, ensuring consistent valve operation without manual adjustments. This automatic zero-lash adjustment happens continuously while the engine runs, creating a more reliable valve train that maintains proper timing throughout the engine’s life. The internal valving system responds to pressure changes, allowing oil to fill the plunger chamber when needed and maintaining a consistent hydraulic cushion that absorbs excess stress in the valve train.
Valve Train Components
Roller-tipped lifters represent the cornerstone of the hydraulic roller camshaft system, offering up to 30% reduction in friction compared to flat tappet designs. These lifters connect to push rods, which transfer motion to rocker arms that eventually open and close the valves. Each component in this chain works harmoniously to create precise valve timing and lift characteristics. The roller tip design allows for more aggressive cam profiles with steeper ramps, creating faster valve opening without excessive component wear. Push rods in these systems typically feature hardened ends to withstand the forces transmitted through the valve train, while the rocker arms pivot smoothly on their mounting points to multiply the lifting force from the camshaft.
Key Benefits of Hydraulic Roller Camshafts
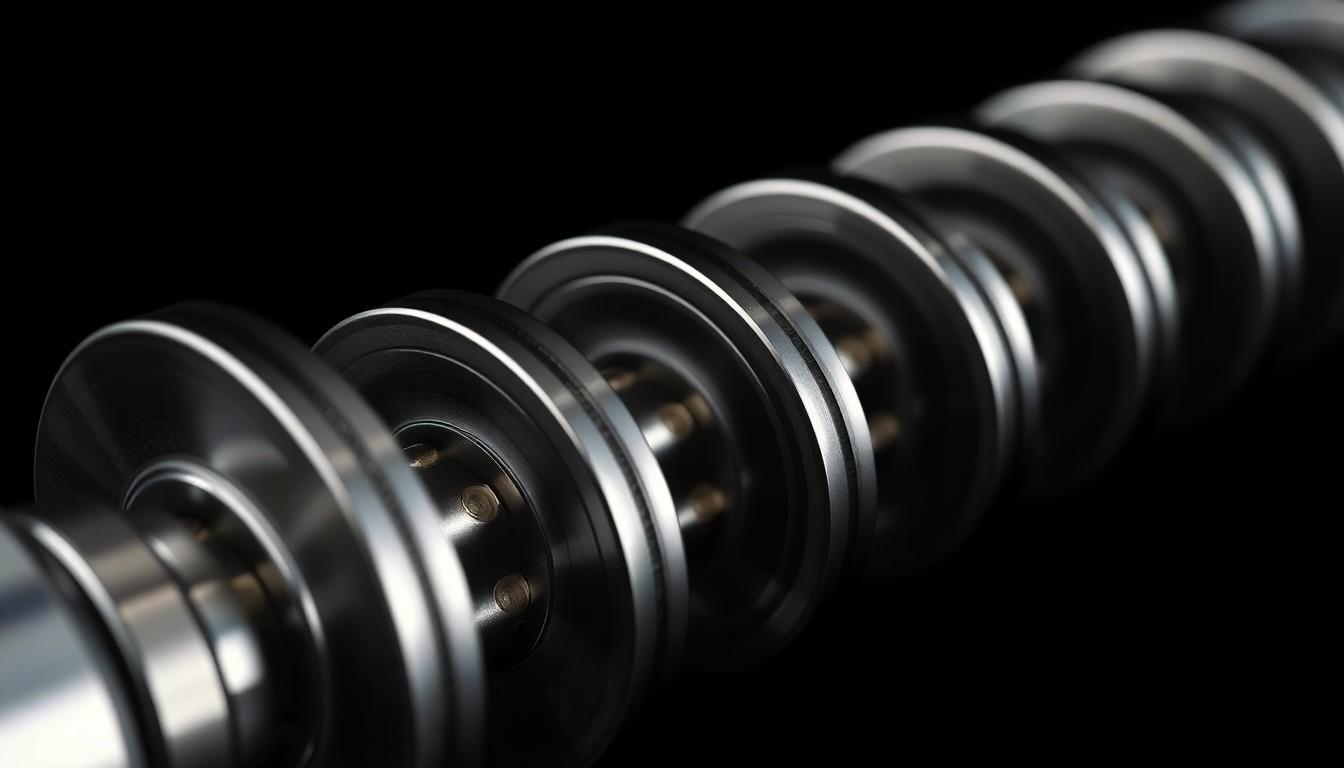
Hydraulic roller camshafts offer important advantages over traditional flat-tappet designs, making them a superior choice for modern engines. These benefits directly impact performance, maintenance, and longevity in ways that matter to both everyday drivers and performance enthusiasts.
Improved Engine Performance
Hydraulic roller camshafts deliver noticeably better engine performance through reduced friction at the cam-to-lifter interface. The roller tips on the lifters decrease frictional losses by up to 20-30%, translating directly into more available horsepower and torque. Engine efficiency improves as this design allows for quicker valve actuation—opening and closing valves more rapidly than traditional designs. Performance enthusiasts particularly appreciate how roller camshafts accommodate more aggressive cam profiles, enabling faster valve opening without the excessive wear associated with flat-tappet designs. These performance gains become especially apparent in high-RPM applications where valve train stability is crucial.
Reduced Maintenance Requirements
The self-adjusting nature of hydraulic roller camshafts eliminates tedious maintenance tasks that plague other camshaft designs. Traditional camshafts require periodic valve lash adjustments—a time-consuming process that demands technical expertise. Hydraulic roller lifters feature internal hydraulic plungers that automatically take up any clearance between components, maintaining optimal valve train operation without manual intervention. This automatic adjustment system creates a quieter engine operation while ensuring consistent performance throughout the engine’s life. Owners appreciate the convenience of never needing to perform valve adjustments, reducing overall maintenance costs and time spent on engine upkeep.
Enhanced Durability
Hydraulic roller camshafts dramatically extend component lifespan through their friction-reducing design. The rolling contact between the lifter and camshaft lobe prevents the metal-on-metal sliding friction that causes rapid wear in flat-tappet systems. This reduced wear pattern protects both the camshaft lobes and the lifters themselves, often extending service life by thousands of miles. Engine builders note that roller camshafts typically maintain their original specifications much longer than their flat-tappet counterparts. Also, the hydraulic element absorbs harmful harmonics and vibrations that would otherwise accelerate component fatigue. These durability improvements make hydraulic roller camshafts particularly valuable in high-performance applications where engine components face extreme stress.
Choosing the Right Hydraulic Roller Camshaft
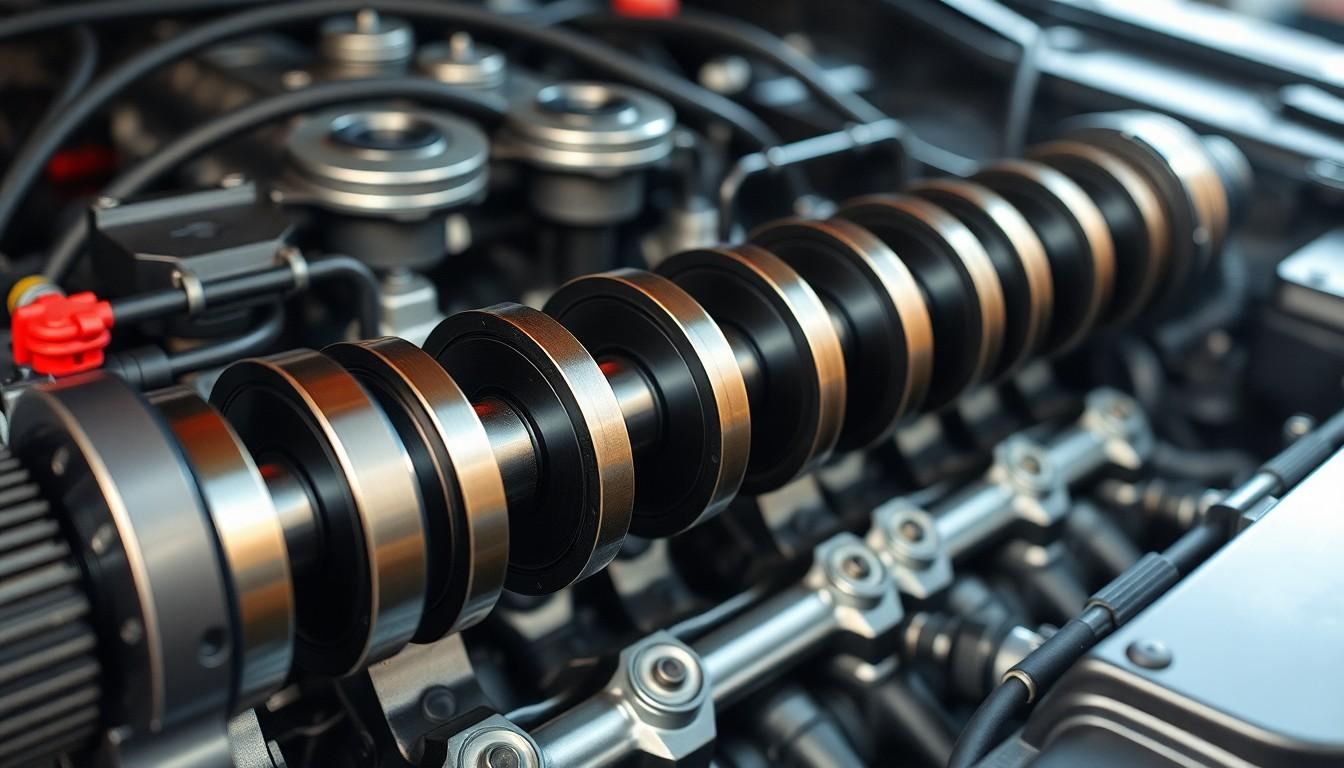
Selecting an appropriate hydraulic roller camshaft transforms your engine’s performance characteristics. The right camshaft matches your exact driving goals, engine specifications, and performance expectations.
Performance Considerations
Performance requirements guide hydraulic roller camshaft selection for optimal results. Cam profile specifications, including duration and lift, directly affect power bands and overall engine behavior. Lobe separation angle influences throttle response, with narrower angles providing quicker response but potentially rougher idle quality. Valve timing events determine where in the RPM range your engine develops peak power—street engines typically benefit from camshafts that prioritize mid-range torque, while race engines often require higher-RPM power development.
Engine displacement and compression ratio impact camshaft selection significantly, as larger engines can use more aggressive cam profiles. Intake and exhaust system modifications must complement your camshaft choice for maximum performance gains. Transmission type matters too—automatic transmissions generally require more conservative cam profiles than manual transmissions to maintain proper torque converter function and drivability.
Installation Requirements
Installation of hydraulic roller camshafts demands precise component matching for reliable operation. Compatible lifters designed specifically for hydraulic roller applications feature roller wheels that align with cam lobes to reduce friction. Proper valve spring pressure proves crucial—springs must provide enough tension to prevent valve float at high RPMs while avoiding excessive pressure that could collapse the hydraulic lifters.
Pushrod length requires careful measurement, as incorrect lengths alter valve train geometry and compromise performance. Rocker arm ratios affect overall valve lift and must be selected to complement your camshaft specifications. Break-in procedures differ from flat tappet cams, with hydraulic roller camshafts typically requiring less complex break-in protocols but still needing proper lubrication during initial startup.
Special retention plates or spider systems keep the roller lifters properly aligned in many engine applications. Engine oil quality remains essential as the hydraulic lifters depend on clean, proper-viscosity oil to function correctly. Computer-controlled engines might need ECU tuning adjustments to accommodate new camshaft specifications, ensuring proper fuel delivery and ignition timing.
Common Applications in Modern Vehicles
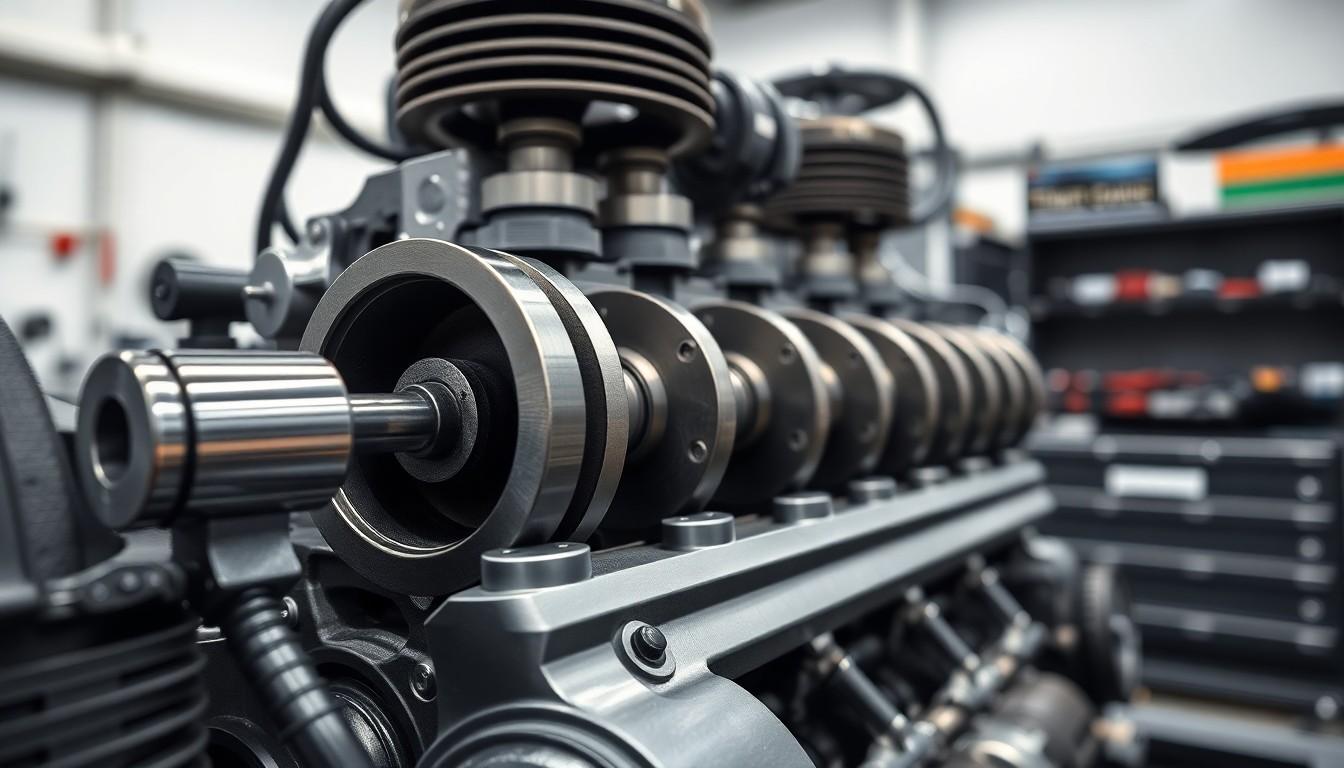
Hydraulic roller camshafts find extensive use in performance vehicles across racing and hot rod communities. Their ability to generate more power while simultaneously reducing wear on critical engine components makes them particularly valuable in high-stress applications. Many professional race teams rely on these camshafts to maximize engine output during competitions where every horsepower counts.
Modern production engines frequently incorporate hydraulic roller technology due to its efficiency advantages and reduced maintenance requirements. Compared to older solid lifter setups, these camshafts provide more consistent valve timing throughout the engine’s operational life, eliminating the need for periodic adjustments that were once standard maintenance procedures. Engine manufacturers appreciate how these systems help vehicles meet increasingly stringent emissions and efficiency standards.
LS and LT series engines represent perfect examples of platforms that benefit significantly from hydraulic roller camshafts. These popular GM powerplants have become the foundation for countless performance builds, from mild street cars to extreme racing applications. The adaptability of hydraulic roller systems allows enthusiasts to select camshaft profiles that match their exact performance goals without compromising reliability or daily drivability.
Conclusion
Hydraulic roller camshafts represent a important advancement in engine technology that delivers tangible benefits for everyday drivers and performance enthusiasts alike. Their innovative design dramatically reduces friction while providing more precise valve control and eliminating maintenance headaches.
Whether you’re looking to upgrade your daily driver or build a competition engine the self-adjusting mechanism and roller-tipped lifters create the foundation for reliable performance and extended component life.
We’ve seen how these systems have revolutionized modern engines by allowing more aggressive cam profiles without sacrificing durability. The technology continues to evolve making hydraulic roller camshafts an essential component in today’s high-performance automotive industry.
Frequently Asked Questions
What is a hydraulic roller camshaft?
A hydraulic roller camshaft is a modern engine component that combines hydraulic lifters with roller tips to optimize valve operation. It uses oil pressure to automatically maintain zero valve lash, which reduces friction and wear compared to older flat-tappet designs. This technology is essential for improving engine performance and longevity in both everyday vehicles and high-performance applications.
How do hydraulic roller camshafts improve engine performance?
Hydraulic roller camshafts improve engine performance by reducing friction at the cam-to-lifter interface by 20-30%. This allows for quicker valve actuation, more aggressive cam profiles, and better power delivery. The reduced friction translates to improved horsepower, torque, and fuel efficiency. Additionally, the design enables faster valve opening without excessive wear, maximizing engine output.
Do hydraulic roller camshafts require frequent maintenance?
No, hydraulic roller camshafts require significantly less maintenance than traditional designs. Their self-adjusting nature eliminates the need for periodic valve lash adjustments. The hydraulic lifters automatically maintain optimal valve clearance using engine oil pressure, ensuring consistent performance throughout the engine’s life. However, maintaining proper oil quality remains important for the system’s longevity.
When did hydraulic roller camshafts become mainstream?
Hydraulic roller camshafts became mainstream in the 1980s, replacing the older flat tappet designs that were once standard in most engines. This transition marked a significant advancement in engine technology, dramatically reducing friction and extending component life. Since then, they have become the preferred choice in modern production engines and performance applications.
How do I choose the right hydraulic roller camshaft for my engine?
Choose the right hydraulic roller camshaft by considering your specific driving goals, engine specifications, and performance expectations. Key factors include cam profile specifications (duration, lift, and lobe separation angle), engine displacement, compression ratio, and intended use (street, racing, or mixed). Component matching is crucial—ensure compatibility with your valve springs, pushrods, and rocker arms for optimal performance.
Are hydraulic roller camshafts better for racing applications?
Yes, hydraulic roller camshafts are excellent for racing applications. They allow for more aggressive cam profiles and quicker valve motion while reducing friction and wear. This results in significant power gains, especially at higher RPMs. Many professional race teams use hydraulic roller camshafts to maximize engine output while maintaining reliability under extreme conditions.
What installation requirements should I be aware of?
When installing a hydraulic roller camshaft, ensure precise component matching, proper valve spring pressure, and careful measurement of pushrod lengths. The installation may require specialized tools and knowledge. For computer-controlled engines, ECU tuning adjustments might be necessary to accommodate new camshaft specifications. Professional installation is recommended for those without extensive engine building experience.
How do hydraulic roller lifters work?
Hydraulic roller lifters work using a self-adjusting system that maintains optimal valve clearance. They feature a roller tip that contacts the camshaft lobe, significantly reducing friction. Inside the lifter, a plunger and check valve system uses engine oil pressure to eliminate lash between components. This continuous adjustment ensures reliable valve operation and proper timing throughout the engine’s life.