Ever wondered what powers your car’s engine with such precision? It’s the humble piston—a mechanical marvel that converts explosive energy into motion. We’ll explore the intriguing area of pistons, from cast aluminum to forged steel varieties, and uncover how these critical components are manufactured.
The manufacturing process of pistons is a blend of engineering excellence and metallurgical mastery. Whether they’re cast in molds, forged under immense pressure, or precision-machined to exacting tolerances, each production method yields pistons with unique characteristics suited for exact applications. In today’s article, we’ll break down the different types of pistons and the sophisticated processes that bring them to life.
Understanding Pistons: Essential Components of Engines
Pistons serve as the heart of an internal combustion engine, converting the energy from fuel combustion into mechanical motion. These cylindrical components move up and down within the engine cylinder, transferring force from expanding gases to the crankshaft through the connecting rod. Without properly functioning pistons, an engine simply couldn’t operate.
The design of a piston includes several critical features that enhance its performance and durability. The piston head (or crown) comes in various configurations optimized for different combustion patterns, including flat-top, dome, and dish designs. Piston rings seal the combustion chamber and prevent oil from entering, while also managing heat transfer from the piston to the cylinder wall. The piston pin (or wrist pin) connects the piston to the connecting rod, allowing the linear motion to be transformed into rotational force.
Materials used in piston manufacturing directly impact engine performance characteristics. Aluminum alloys provide excellent heat conductivity and lighter weight, making them ideal for high-performance applications. Cast iron pistons offer superior durability but add important weight to the engine. Composite pistons combining materials like aluminum with steel reinforcements deliver a balance of strength and weight advantages in specialized applications.
Modern piston development focuses on reducing friction, improving thermal efficiency, and extending service life. Engineers apply special coatings to reduce friction between the piston and cylinder walls. Advanced cooling systems within pistons help manage the extreme temperatures experienced during combustion. Computer modeling allows manufacturers to optimize piston designs for exact engine requirements, creating components that balance performance, efficiency, and longevity.
Different Types of Pistons in Modern Engineering
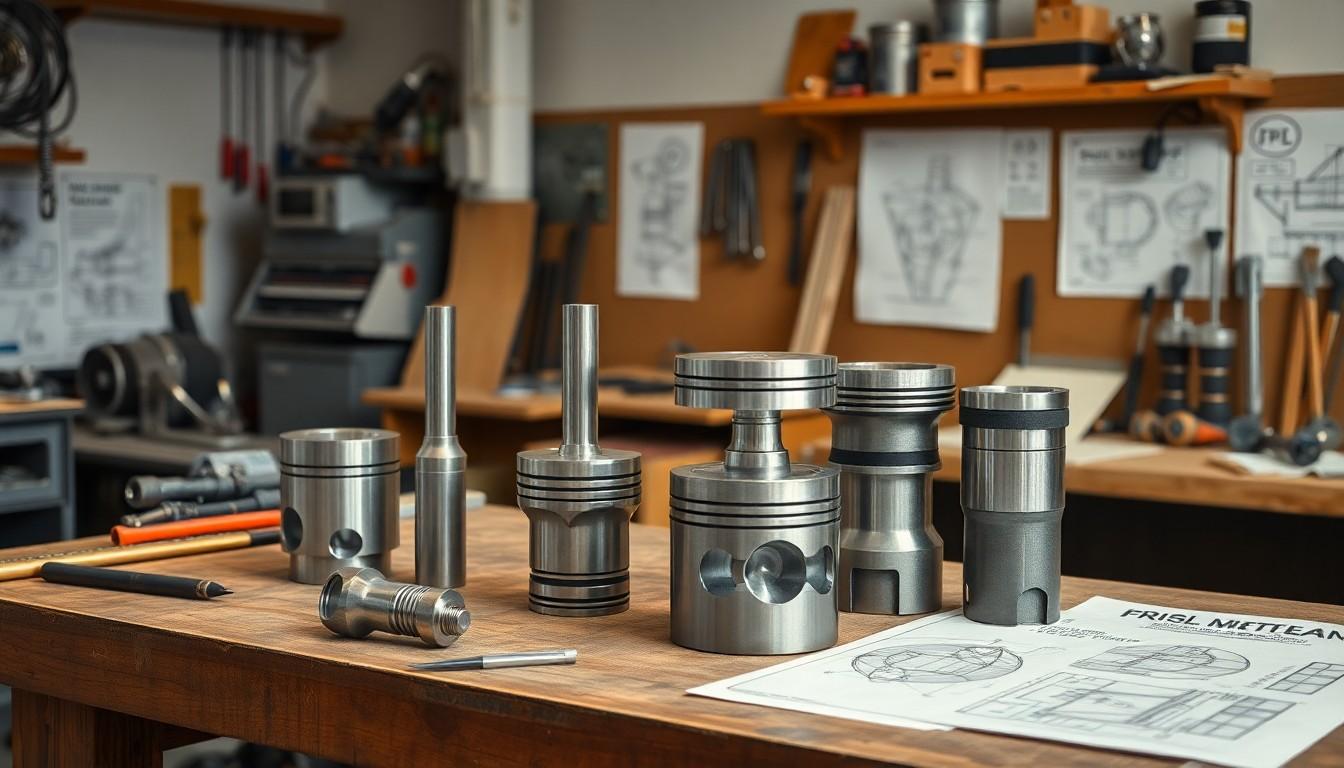
Modern engineering utilizes several distinct piston designs, each with exact characteristics optimized for particular applications. These varied designs address different performance requirements across various engine types and operational conditions.
Trunk Pistons
Trunk pistons feature a long length relative to their diameter, serving dual functions as both a piston and cylindrical crosshead. This design effectively supports side forces generated by angled connecting rods against cylinder walls. Historically used in both petrol and diesel engines, trunk pistons are gradually being replaced by lighter alternatives in high-speed applications. A distinctive characteristic of trunk pistons in diesel engines is an additional groove for an oil ring positioned below the gudgeon pin, complementing the rings located between the gudgeon pin and crown.
Crosshead Pistons
Crosshead pistons represent a historically important design, particularly in traditional marine steam engines. Unlike integrated designs, these pistons incorporate a separate crosshead connected to the piston rod. Modern internal combustion engines rarely use the term “crosshead piston,” as contemporary focus has shifted toward other designs like trunk, slipper, and deflector variants. The historical importance of crosshead pistons remains relevant for understanding piston design evolution, even though their limited presence in current applications.
Slipper Pistons
Slipper pistons are engineered for minimal weight with reduced skirt areas, delivering lower friction and overall mass. Racing engines particularly benefit from these lightweight designs, which maximize RPM potential and performance capabilities. The compact construction of slipper pistons contributes to reduced engine weight compared to traditional alternatives. This weight-saving advantage comes with a trade-off, as durability may be sacrificed to achieve optimal performance characteristics in high-revving applications.
Deflector Pistons
Deflector pistons incorporate specialized crown shapes designed to redirect fuel mixtures away from cylinder walls toward combustion chamber centers. This strategic deflection improves combustion efficiency while reducing emissions through optimized fuel-air interaction. Diesel engines commonly use these pistons to enhance fuel injection system performance, creating more complete mixing and combustion processes. The crown’s distinctive shape plays a crucial role in controlling combustion dynamics, particularly in compression ignition applications where precise fuel distribution significantly impacts performance and emissions.
Materials Used in Piston Manufacturing
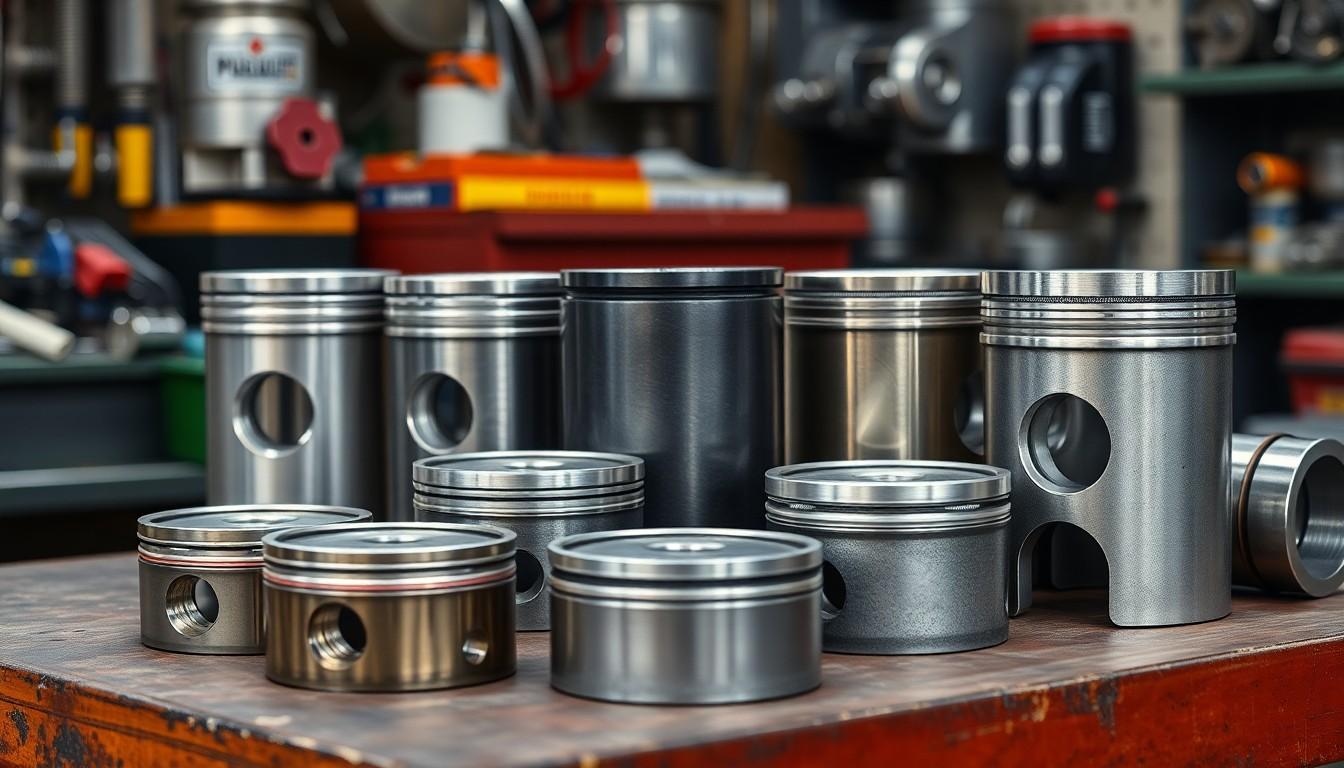
Piston materials significantly impact engine performance, durability, and efficiency. The right material choice depends on the exact application, operating conditions, and performance requirements of the engine.
Aluminum Alloy Pistons
Aluminum alloy pistons dominate modern engine designs due to their exceptional weight-to-strength ratio. These pistons effectively reduce the overall engine weight while providing excellent thermal conductivity that helps dissipate heat more efficiently. Manufacturing processes for aluminum pistons include both casting and forging techniques, with each offering distinct advantages. Aluminum’s lightweight properties contribute directly to improved fuel efficiency and reduced reciprocating mass, allowing engines to operate at higher RPMs with less strain on connecting components. Engine manufacturers often choose aluminum alloys containing silicon, copper, and magnesium to enhance exact performance characteristics like thermal stability and wear resistance.
Cast Iron Pistons
Cast iron pistons excel in durability and heat resistance, making them suitable for exact high-stress applications. These pistons demonstrate superior wear characteristics compared to aluminum variants, particularly in environments with minimal lubrication. The excellent thermal characteristics of cast iron allow these pistons to operate effectively in extreme heat conditions without deformation. Cast iron’s natural damping properties help reduce noise and vibration in certain engine configurations. Even though their advantages, cast iron pistons weigh significantly more than aluminum alternatives, creating additional stress on the connecting rod and crankshaft components.
Steel Pistons
Steel pistons offer exceptional strength and durability for specialized heavy-duty applications where performance outweighs weight considerations. These pistons provide superior resistance to deformation under extreme pressure, making them ideal for certain high-performance diesel engines. Steel’s lower thermal expansion rate compared to aluminum creates more consistent piston-to-cylinder clearances across varying operating temperatures. Manufacturing processes for steel pistons typically involve sophisticated forging techniques followed by precise machining operations. The weight disadvantage of steel pistons can be partially offset by innovative designs featuring thinner walls and reinforced stress points, maintaining strength while reducing overall mass.
The Piston Manufacturing Process
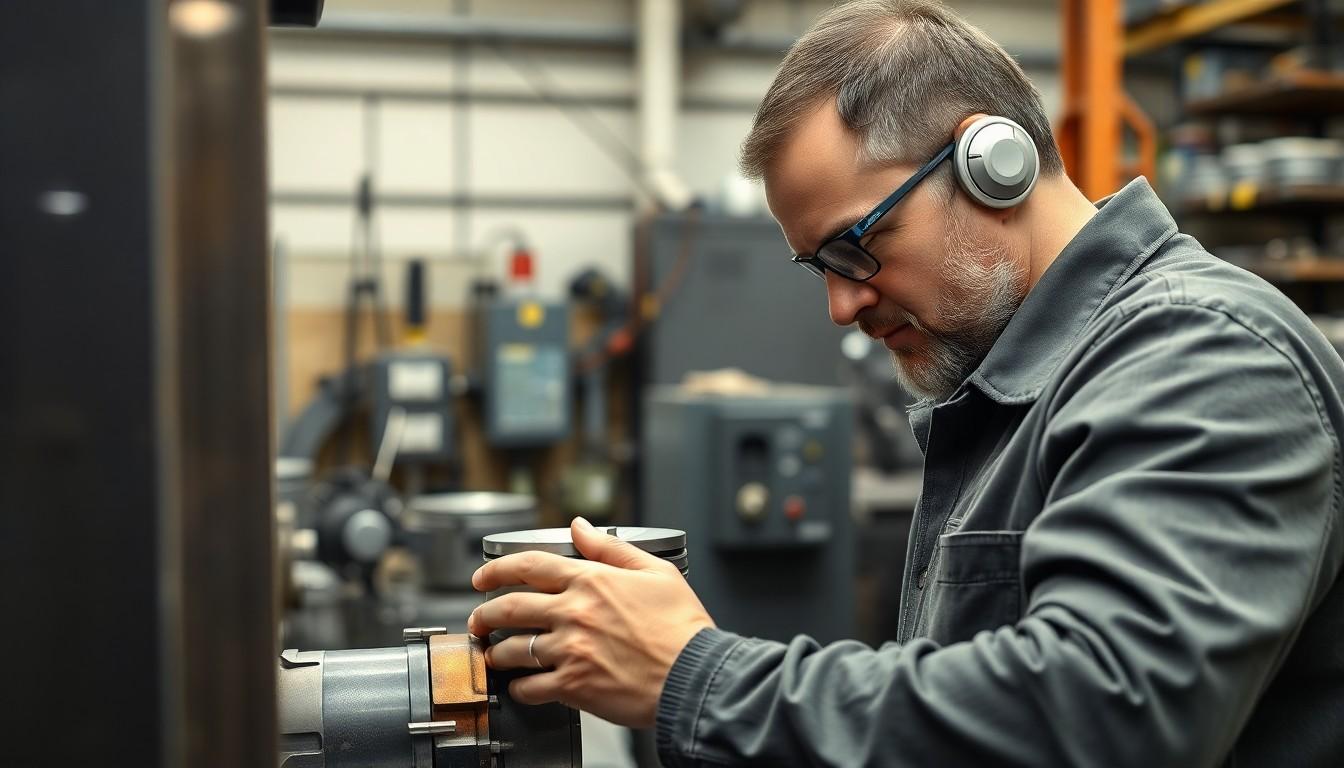
Piston manufacturing combines precision engineering with metallurgical expertise to create components that can withstand extreme conditions. Modern production techniques have evolved to balance cost-effectiveness with performance requirements across various engine applications.
Casting Methods
Cast pistons emerge from a process where molten metal (typically aluminum or cast iron) flows into specially designed molds. This method represents the most economical approach to piston production while still delivering adequate performance for many applications. Hypereutectic cast pistons contain higher silicon percentages—often between 16-18%—which enhances their strength and durability compared to conventional cast alternatives. The silicon crystals within these pistons provide improved wear resistance and thermal stability, making them suitable for moderate-performance engines without the premium cost of forged options.
Forging Techniques
Forged pistons result from applying tremendous pressure to heated metal billets, creating a denser, stronger component with aligned grain structure. This manufacturing technique delivers superior strength-to-weight ratios by compressing the metal’s molecular structure and eliminating potential weak points or voids. Forged pistons handle higher temperatures, greater pressures, and more aggressive driving conditions than their cast counterparts. Racing engines, high-performance vehicles, and heavily modified street cars commonly use forged pistons even though their higher cost because they can withstand extreme conditions like higher RPMs, forced induction, and nitrous oxide systems.
CNC Machining and Finishing
CNC machining transforms raw cast or forged piston blanks into precisely engineered components with tolerances measured in micrometers. Computer-controlled cutting tools remove excess material to create the final profile, including valve reliefs, ring grooves, and oil return channels. Advanced finishing processes such as grinding optimizes the cylindrical surfaces for perfect cylinder wall contact, while honing creates microscopic crosshatch patterns that retain oil films for improved lubrication. Surface treatments like anodizing, Teflon coating, or phosphate finishing can further enhance durability by increasing hardness, reducing friction, and improving heat dissipation. The quality of these finishing operations directly impacts piston longevity, noise levels, and overall engine performance.
Quality Control and Testing in Piston Production
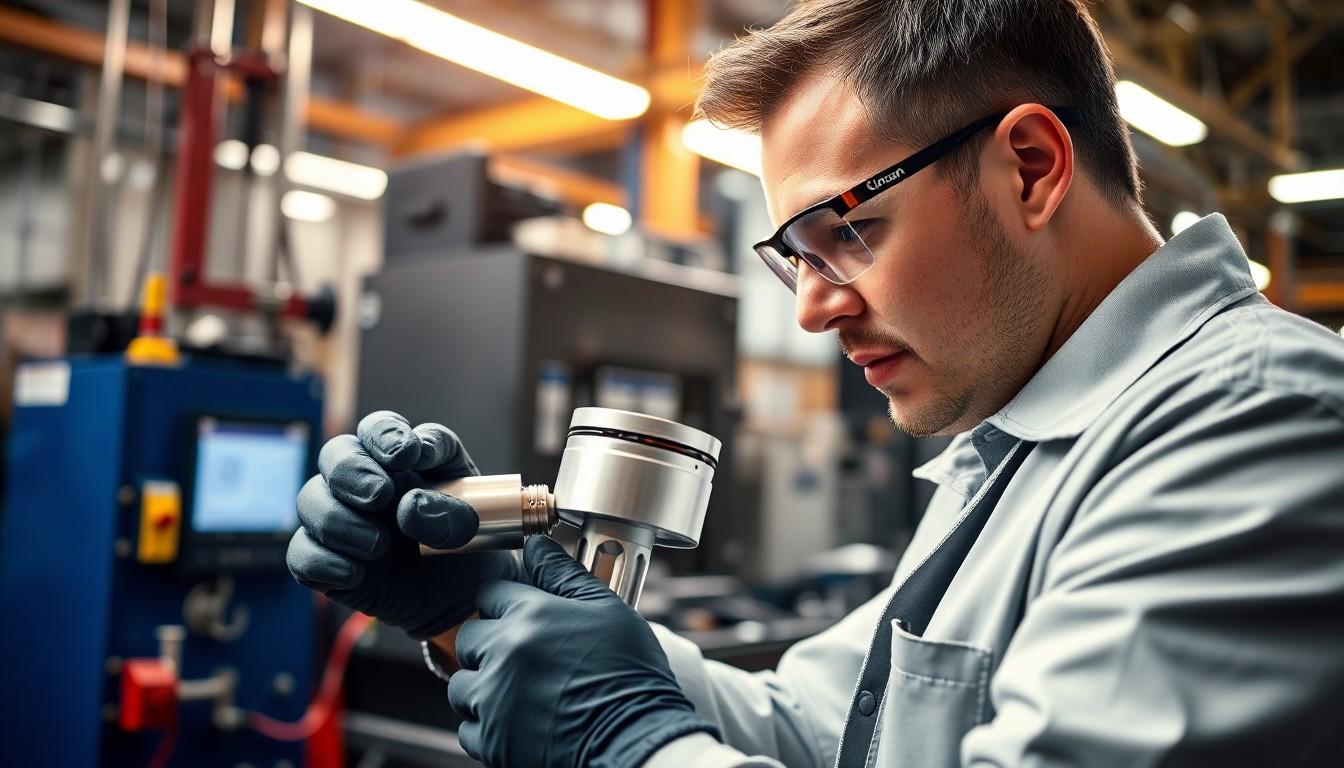
Quality control and testing represent critical stages in piston manufacturing that ensure each component meets stringent performance standards before installation in an engine. These processes safeguard reliability and longevity in real-industry applications where pistons face extreme conditions.
Key Steps in Quality Control
Material inspection forms the foundation of quality control, verifying that raw materials meet specified standards before entering the production line. Dimensional checks follow throughout manufacturing, using precision measurement tools to confirm exact specifications are maintained across all critical dimensions.
Surface finish inspection identifies any imperfections that might compromise performance or durability under high-stress conditions. Strength and durability testing subjects pistons to simulated stresses, assessing their ability to withstand the punishing environment of an internal combustion engine.
Leak testing detects any potential flaws that could allow gas or oil passage, compromising engine efficiency and performance. Visual inspection by trained technicians serves as a final verification step to catch any visible defects before pistons advance to the next production phase.
Testing Methods
Ever-changing testing evaluates pistons under simulated engine conditions, providing real-industry performance data about how they’ll function when installed. Static testing measures fundamental properties like compression resistance and tensile strength, establishing baseline performance metrics for each piston.
Non-destructive testing (NDT) techniques including ultrasonic scanning and X-ray inspection reveal internal flaws without damaging the pistons themselves. These advanced methods detect hidden inconsistencies in material density or structure that might lead to premature failure.
Manufacturers increasingly employ computer-aided analysis alongside physical testing to predict piston behavior under various operational scenarios. This comprehensive approach to quality control ensures only pistons meeting all performance criteria make their way into engines, delivering reliable performance throughout their service life.
Innovations and Future Trends in Piston Technology
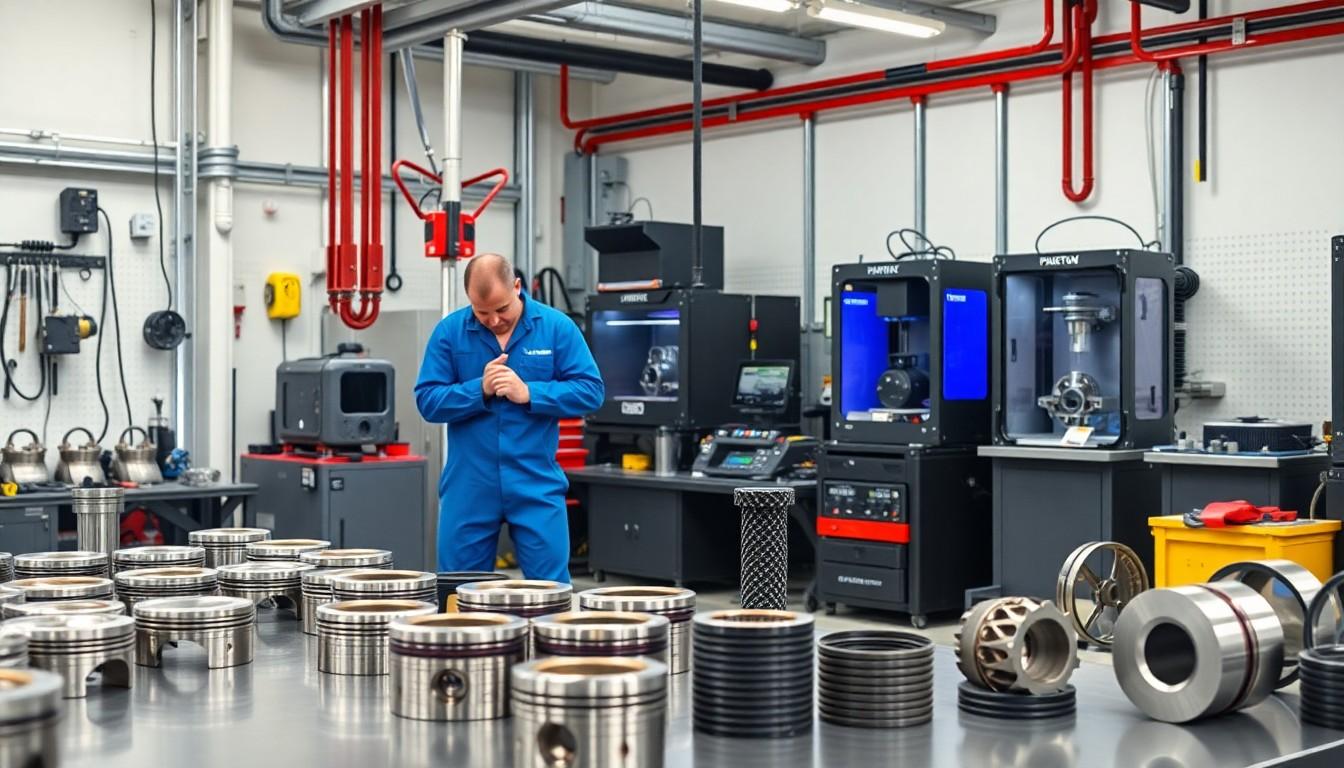
Advanced Materials
Advanced materials represent a important frontier in piston innovation. Lightweight alloys and composite materials are revolutionizing piston performance while reducing overall weight. These materials contribute to enhanced fuel efficiency by decreasing reciprocating mass within the engine. Manufacturers are exploring aluminum matrix composites that offer superior strength-to-weight ratios compared to traditional alloys. Carbon fiber reinforced pistons have emerged in racing applications, demonstrating the potential for even lighter engine components with excellent thermal properties.
Coatings and Surface Treatments
Coatings and surface treatments have transformed modern piston technology. Ceramic coatings create thermal barriers that improve heat management within combustion chambers. Nano-coatings reduce friction between pistons and cylinder walls, minimizing power loss and extending engine life. Diamond-like carbon (DLC) treatments provide exceptional wear resistance while maintaining low friction coefficients. These advancements result in measurable gains in engine efficiency, often increasing power output while reducing fuel consumption by 2-5% in optimized designs.
3D Printing
3D printing technology is completely changing piston manufacturing approaches. Complex geometries previously impossible to machine can now be produced with precise dimensional control. Custom designs customized to exact engine applications eliminate compromises inherent in mass production. Additive manufacturing enables internal cooling channels and variable wall thicknesses that optimize weight and strength characteristics. Production costs are decreasing as 3D printing technology matures, making customized pistons more accessible for specialized applications beyond racing and prototype development.
Hybrid and Electric Vehicle Applications
Hybrid vehicle technologies have created new demands for piston innovation. Variable compression ratio pistons adapt to different operating conditions in hybrid powertrains. Special heat-resistant materials address the unique thermal challenges of engines that frequently stop and restart. Pistons designed for hybrid applications often incorporate enhanced oil control features to maintain lubrication during extended idle periods. While fully electric vehicles eliminate traditional pistons entirely, range-extended electric vehicles continue to benefit from advanced piston designs that maximize efficiency during generator operation.
Conclusion
The evolution of piston technology showcases remarkable engineering ingenuity. From diverse piston types designed for exact applications to advanced manufacturing processes involving casting forging and precision machining we’ve seen how these critical components are meticulously crafted.
Materials science plays a pivotal role with aluminum alloys cast iron and steel each offering unique performance characteristics. The rigorous quality control ensures reliability while innovations in coatings surface treatments and 3D printing point to an exciting future.
As engines continue to evolve so will pistons adapting to new demands for efficiency power and sustainability. The humble piston remains at the heart of internal combustion technology a testament to engineering excellence that powers our industry forward.
Frequently Asked Questions
What is the primary function of a piston in a car engine?
A piston converts explosive energy into motion within an engine. It moves up and down inside the cylinder, transferring force from expanding gases to the crankshaft. This reciprocating motion is fundamental to the operation of internal combustion engines, effectively transforming fuel combustion into mechanical energy that powers the vehicle.
What materials are commonly used to make pistons?
Pistons are primarily made from aluminum alloys, cast iron, and steel. Aluminum alloys dominate modern designs due to their excellent weight-to-strength ratio and thermal conductivity. Cast iron pistons offer superior durability and heat resistance for high-stress applications, while steel pistons provide exceptional strength for heavy-duty engines.
How are pistons manufactured?
Pistons are manufactured through casting, forging, and precision machining processes. Casting involves pouring molten metal into molds to create economical pistons. Forging applies pressure to heated metal for stronger, denser pistons ideal for high-performance applications. CNC machining then achieves precise tolerances, followed by surface treatments to enhance durability.
What are the main types of pistons used in modern engines?
Modern engines use several piston types: trunk pistons (standard in most engines), crosshead pistons (historically used in marine engines), slipper pistons (lighter designs with reduced friction for racing applications), and deflector pistons (optimized for diesel engines to enhance combustion efficiency). Each type is designed for specific performance requirements and engine applications.
What quality control measures ensure piston reliability?
Piston quality control involves material inspection, dimensional checks, surface finish evaluation, strength testing, leak testing, and visual inspection. Manufacturers use static testing and non-destructive testing (NDT) to simulate engine conditions. Computer-aided analysis complements physical testing to ensure only pistons meeting stringent performance standards are used in engines.
How are pistons evolving with new automotive technologies?
Piston technology is advancing with lightweight alloys, composites, ceramic and nano-coatings that improve heat management and reduce friction. 3D printing enables creation of complex designs with reduced production costs. As hybrid and electric vehicles evolve, innovative piston designs are being developed to adapt to new operating conditions and enhance efficiency.
What key design features do pistons have?
Pistons feature several critical design elements: the piston head (which withstands combustion pressure), piston rings (which seal the combustion chamber and control oil), and the piston pin (which connects to the connecting rod). These components are carefully engineered to enhance performance, durability, and efficiency within specific engine applications.
Why are aluminum alloy pistons so common in modern engines?
Aluminum alloy pistons dominate modern engine designs because they offer an excellent weight-to-strength ratio and superior thermal conductivity. Their lighter weight improves fuel efficiency and allows engines to reach higher RPMs. Additionally, aluminum’s thermal properties help dissipate heat effectively, which is crucial for engine performance and longevity.